views
At its core, a laser beam welding tool is a high-precision device that employs a concentrated beam of laser light to join materials, typically metals. The laser acts as a heat source, melting the edges of the material so they can fuse together. What makes this process stand apart is its focus and intensity—the beam is so narrow and concentrated that it produces a small, high-energy heat zone capable of deeply penetrating even the toughest metals.
The term “laser” stands for Light Amplification by Stimulated Emission of Radiation. In the context of welding, it’s more than just a beam of light—it's a finely tuned tool that can slice through or fuse metals with unmatched accuracy.
How Does It Actually Weld Without Touch?
The idea of welding without contact might seem puzzling at first. Traditionally, welding involves electrodes, arcs, or gas torches that physically interact with the workpiece. However, the laser beam welding tool changes that dynamic entirely. Here's how:
-
Energy Absorption: The laser beam is directed toward the surface of the metal. When the light hits the metal, the material absorbs the energy and heats up rapidly.
-
Melting Point: The localized heating causes the metal to reach its melting point in milliseconds.
-
Fusion: As the beam moves along the joint, the molten edges fuse together and then solidify almost instantly, forming a clean, solid bond.
All of this happens without the need for physical contact between the tool and the workpiece. This makes the process not only clean but also highly efficient and suitable for delicate components.
Applications Across Industries
The laser beam welding tool isn’t just a high-tech novelty—it’s a staple in several cutting-edge industries. Here's where it's making a substantial impact:
Automotive Manufacturing
From chassis components to fuel injection systems, the automotive industry demands high-speed, precision welding. The laser beam welding tool is extensively used to join different grades of steel and aluminum in automotive assemblies. Its deep penetration and narrow weld zones are perfect for complex car parts.
Aerospace Engineering
The aerospace sector relies on lightweight, high-strength alloys that require careful handling. The precision of laser beam welding is ideal for fabricating turbine blades, fuel systems, and structural components. Since the process introduces minimal thermal distortion, it ensures dimensional accuracy, which is vital in aviation.
Medical Device Fabrication
In the world of medical equipment, cleanliness and precision can be a matter of life and death. Surgical instruments, implants, and micro-scale components are often assembled using laser beam welding tools. The non-contact nature of the process helps maintain hygiene standards while delivering microscopic precision.
Electronics and Microengineering
Micro-welding in electronics is another domain where laser beam welding tools shine. Whether it’s battery terminals, sensors, or delicate wire connections, these tools offer unmatched control for creating micro-welds without damaging the surrounding components.
Tool and Die Industry
In mold and die repair, laser welding is used to fix defects or enhance tool life. The laser beam welding tool allows operators to add precise amounts of material to worn or damaged areas, restoring tools without compromising their original dimensions.
Why It Has Revolutionized Metal Joining
The term “revolutionary” gets thrown around a lot in industrial circles, but the laser beam welding tool truly earns the title. Here's why:
-
Contactless Operation: Since there’s no need for physical contact, wear and tear on the welding tool are significantly reduced.
-
Precision Control: The laser can be focused to within microns, allowing for delicate welds that are otherwise impossible with conventional methods.
-
High-Speed Performance: With the ability to complete welds in milliseconds, production cycles are faster, and throughput increases substantially.
-
Adaptability: Whether it’s stainless steel, titanium, or exotic alloys, the laser beam welding tool can handle a wide range of materials.
The Science Behind the Tool
Understanding how the laser beam welding tool works involves a bit of physics. Lasers emit light in a coherent beam—meaning the light waves are in phase and move in the same direction. This coherence is what gives the laser its immense power density.
When this concentrated light is directed at a metal surface:
-
Absorption: Metals like steel or aluminum absorb the light energy depending on their wavelength compatibility with the laser type.
-
Heating and Melting: The absorbed energy increases the temperature rapidly, causing the material to melt locally.
-
Fusion Zone: As the beam moves, the molten area follows, creating a continuous weld pool that solidifies into a seam.
Different types of lasers are used depending on the application—CO₂ lasers, fiber lasers, and Nd:YAG lasers are the most common types employed in laser beam welding tools.
Considerations in Practical Use
While the laser beam welding tool offers exceptional results, its successful implementation requires meticulous planning and calibration. Here are a few practical considerations:
-
Beam Focus: The distance between the laser lens and the workpiece must be precise to ensure a proper focus and consistent energy delivery.
-
Shielding Gas: Although it’s a clean process, shielding gases like argon or helium are often used to protect the weld area from oxidation.
-
Joint Fit-Up: The pieces to be joined must have an accurate fit since laser welding doesn’t involve filler material in most cases.
Integration with Automation
One of the most powerful aspects of the laser beam welding tool is its seamless integration with automated systems. Robotic arms equipped with laser welders are now a common sight in advanced manufacturing plants. This allows for:
-
Greater consistency in weld quality.
-
24/7 operation without fatigue.
-
Real-time monitoring and quality control.
Additionally, with the emergence of CNC programming and 3D modeling, the entire welding process can be pre-programmed to handle intricate designs with minimal human intervention.
Future Trends and Evolution
The laser beam welding tool continues to evolve with innovations like:
-
Hybrid Welding: Combining laser welding with arc welding to leverage the advantages of both techniques.
-
High-Power Lasers: Newer tools can deliver higher wattage for deeper penetration and thicker materials.
-
Miniaturization: Compact laser welders for use in space-limited environments like cleanrooms or surgical suites.
As industries push for more sustainable, efficient, and miniaturized production methods, the demand for laser beam welding tools is set to grow exponentially.
Final Thoughts
The laser beam welding tool represents a paradigm shift in how industries approach metal joining. From its contactless operation to unmatched precision and adaptability, this tool is transforming the landscape of manufacturing, one weld at a time. Whether you're in automotive production, aerospace design, or medical device engineering, embracing this advanced technology opens the door to a new realm of possibilities. As more sectors integrate laser welding into their workflows, the importance of understanding and leveraging this tool will only continue to rise. The future of metal fabrication is here—and it’s powered by light.
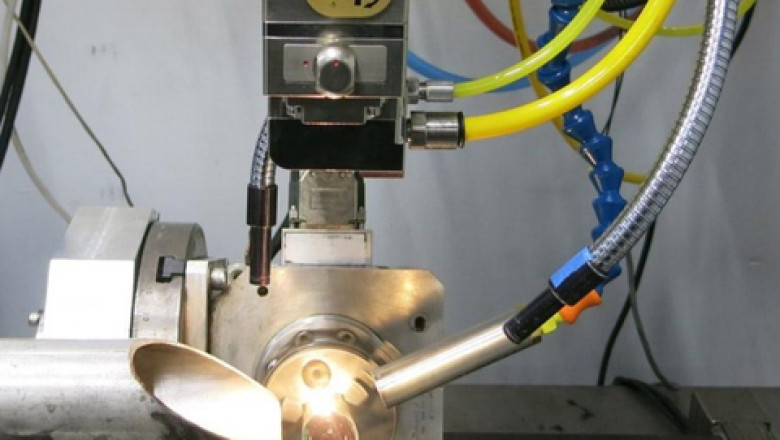

Comments
0 comment